
Cost-cutting Walmart warehouses have back-breaking worker conditions
Paul Harris, The Guardian
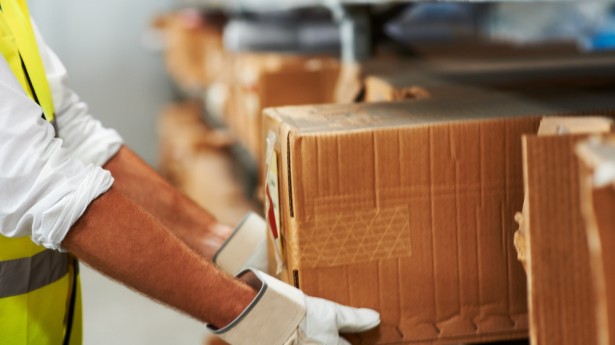
None of the workers loading and unloading Walmart goods at the NFI Crossdock warehouse know exactly what is in the layer of black dust that seems to cover almost everything. But they know its effects.
Their throats burn, and their eyes water. For a few, it gets worse. “I go and blow my nose, and blood comes out with the black dust,” said Jose Gonzalez, pictured, a “lumper” at the warehouse, who shifts several hundred Walmart-bound boxes every hour. “Even blowing my nose in the shower, blood comes out. When you spit, sometimes blood comes out,” Gonzalez added.
Yet the dust is just one complaint at NFI Crossdock, part of a vast network of warehouses clustered in the Inland Empire: a stretch of southern California desert that now lies at the heart of Walmart’s American supply chain.
The NFI Crossdock near the city of Ontario – where lumpers like Gonzalez toil in 100F heat – sits in the middle of a vast lot of trucks, many of them emblazoned with Walmart logos. The warehouse unloads shipping containers arriving at California ports, and loads them again on trucks taking goods to Walmart stores across America. It is back-breaking work, with strict quotas, low wages and few benefits.
Last week a union-backed campaign group, Warehouse Workers United, lodged an official complaint with California labour authorities about conditions at NFI Crossdock, which is operated by NFI, a subsidiary of National Distribution Centers of Delaware. The complaint described vital equipment that is often faulty, old or broken, and that poses a serious risk to health.
Inside the containers – where lumpers sometimes spend several hours at a time – workers say the heat can reach 125F, with little or no quick access to water. Often lights are broken so workers must also toil in the dark. Workers must even buy their own safety equipment from a company store. Injuries are common, as managers pressure workers to lift hundreds of boxes an hour.
The complaint also detailed the dust, describing workers vomiting and coughing blood. “You walk in there. But you don’t know if you will walk out,” Apolinar Rojas, a forklift driver recently injured in an accident while driving his vehicle, told the Guardian.
An NFI spokesperson has denied the allegations in the complaint, saying they were “riddled with fallacies”. The firm insists it takes all required safety precautions. “NFI takes workplace safety as well as injury prevention and response extremely seriously,” the spokesperson said.
WWU organisers say the complaint is aimed at protecting some of the most vulnerable workers in America. It also adds to a current focus on how Walmart brings goods to its thousands of US stores.
‘They run out of places to squeeze the costs’
While much recent attention has focused on abuses at the outsourced Chinese supply chains of companies like Apple, some experts believe Walmart’s US-based supply chain is built on a similar model, but one constructed within America US itself.
As is common in China, the supply chain is marked by layers upon layers of subcontracting. So, while every single box packed and unpacked at NFI Crossdock is destined for Walmart, the warehouse is owned, run and staffed by myriad other companies. The supply model has been dubbed “insourcing”, and experts say it is defined by ruthless cost-cutting as each layer of subcontracting seeks to eke out a profit margin.
“Walmart’s suppliers run out of places to squeeze out the costs, and they are left with the workers,” said Catherine Ruckelshaus, co-author of a recent report on the supply chain called Chain of Greed, that was produced by the National Employment Law Project.
Walmart is not the only big-box retailer supplied by the huge warehouses of the Inland Empire. Other major firms, such as K-Mart, Home Depot and Toyota, also work there. But Walmart sets the model for the others by its sheer size.
The impact of the immense pressure on Walmart suppliers can easily be seen at what workers call simply “the Crossdock”. Workers say they are given brutal quotas for the number of boxes that they need to shift each hour. Supervisors, they say, make it clear that any failure to meet those quotas – even at the risk of physical injury – could be the loss of a job. “I feel that I am just something they could use and throw away,” said Limber Herrera, 29, pictured, who is supporting a wife and two children on his wage.
Few of those working the Crossdock can afford to lose the work: even when it comes at the price it does. Take Reuben Valdez. He is 61, and lives in a cheap motel with his partner and her mother, who suffers from dementia. He lost his home after supervisors reduced his hours, causing him to miss rent payments. He is desperate, recently pawning jewellery to pay for three more nights at an Econo Lodge.
Despite his age, Valdez says he is expected to meet quotas of up to 250 boxes an hour. “It is an impossibility. But they tell you to work harder. They shout at you and harass you. They say: ‘If you can’t take it, then you know where the door is,’” he said.
‘I am so annoyed and aggravated’
There would be no shortage of people to replace him. Over the last 10 years the warehouse industry has boomed in the Inland Empire. This stretch of hot and dry desert valley, about an hour’s drive from Los Angeles, is now the biggest such hub in America. It is thought that about 110,000 low-wage warehouse workers are now employed in the Inland Empire, with the vast majority of them being Hispanics, and around half being immigrants.
One recent survey by the WWU and the University of California interviewed 101 workers and found that 83 of them said they had suffered a job-related illness. It also found that almost half of workers claimed to have been exposed to chemicals at work. All told the Inland Empire’s warehouse workers represent one of the most vulnerable work forces in America: low paid, afraid to speak out, and with virtually no political power.
Some workers complain of the mental stress caused by these conditions. “There are times that I can’t go straight home because I am so annoyed and aggravated. I just have to stay outside,” said Carlos Martinez, 27, pictured.
Others blame the pressure for causing injuries, which they say supervisors see as an inconvenience and a threat to slowing the processing of goods. They describe a system run by fear. When Rojas was injured on the job, he says, he was told to finish his quota before seeking medical help. He then had to walk two miles to a clinic, but found it shut by the time he arrived. He returned to work and only then was sent to a 24-hour clinic where he was diagnosed with a sprained back, neck and shoulder.
The NFI Crossdock is hardly alone, however. Other warehouses serving the Walmart supply chain in the Inland Empire have also had problems. At a warehouse run by a subcontracted firm called Schneider – barely a mile away from NFI Crossdock – a class action lawsuit has alleged that Schneider and two staffing agencies it contracted to supply workers falsified pay records in a way that kept their wages even lower. Workers there also complained of poor safety standards, a climate of fear and being pressurised to work so hard that injuries resulted.
One worker at a Schneider plant – which, like the NFI Crossdock supplied only Walmart – described to NELP how he worked 362 days in a year, for 16 hours a day, with no overtime and no lunch breaks.
Schneider has denied the allegations, saying it complies with labour regulations.
In this supply chain, retaliation for speaking out or complaining is common, workers say. At NFI Crossdock, Rojas described coming back to work after his injury and being given a broom and a chair and told to sit in the middle of the warehouse floor. “I felt like they did it to embarrass and humiliate me. In eight years I have never seen anyone do that,” Rojas said.
‘I can’t tie my shoelace without it hurting’
At Schneider, Marcos Lopez, 19, who is part of the class action claim, suffered a back injury working as a lumper. But, as he reported it more than an hour after feeling the first spasms of pain, he was put on a “performance improvement plan” for late reporting an injury. Shortly afterwards he lost his company ID badge. He was charged $5 to replace it, and fired for losing company property. “I don’t have health insurance, and my back is still messed up. I can’t tie my shoelace without it hurting,” Lopez said told the Guardian.
Walmart says the labour conditions are the responsibility of its contractors. Indeed, the contractors themselves also then often subcontract, especially with staffing agencies who often supply most of the labour for the manual jobs.
Critics say such an argument is disingenuous. “Walmart uses these companies as a buffer to negate any responsibility for what happens in their workplaces,” said Professor Juan de Lara, an expert at the University of Southern California.
In fact, critics say, Walmart’s business strategy is based on inflicting relentless cost-cutting on suppliers. The giant firm builds its supply chain with a “plus one” bargaining strategy, which requires all suppliers and contractors to reduce their price or increase their speed each and every year they work with Walmart.
Walmart also has staff inside the warehouses of the Inland Empire. At NFI Crossdock, there is a Walmart employee on site. Court documents filed as a result of the Schneider suit showed Walmart set productivity standards and – if warehouse worker productivity declined – cut compensation to Schneider.
But there are signs that Walmart is recognising a problem. When it came to the specific points of the complaints of NFI workers, Walmart spokesman Dan Fogleman said: “It’s concerning to hear these types of claims about someone we do business with and, while these are just allegations at this point, we recognize there is an opportunity to step up and help shape the working environment that exists in some of these facilities.
“We hold all of our service providers and their subcontractors to the highest standards, and expect and require them to comply with the law and, if violations occur, to take corrective action immediately.”
Fogleman said the firm was looking to make improvements. “We are looking at a number of ways we can better work with our service providers to help them develop processes to prevent and detect potential issues and help ensure the people working for them are treated appropriately,” he added.
That might be a glimmer of hope for labour activists. “The same way Walmart drives down standards, they can also make this a better industry,” said Guadalupe Palma, a campaign director with WWU. De Lara argued that the warehouse industry could actually form part of a US economic recovery if wages were higher. “They don’t have to be bad jobs. They can support a decent middle-class lifestyle,” he said.
However, there is still a long way to go. Recently, in response to the WWU efforts in the warehouses, supervisors at NFI Crossdock handed many workers a flyer with their wages. The leaflet, a copy of which was obtained by the Guardian, warned against supporting the formation of a union. “Don’t sign away your rights,” it claimed.
One recipient of the flyer was Miguel Gonzalez. He was told to make sure he read it by a woman manager, but warned against doing so on company time when he should be lifting boxes. “She said I needed to read it on my break,” Gonzalez said.